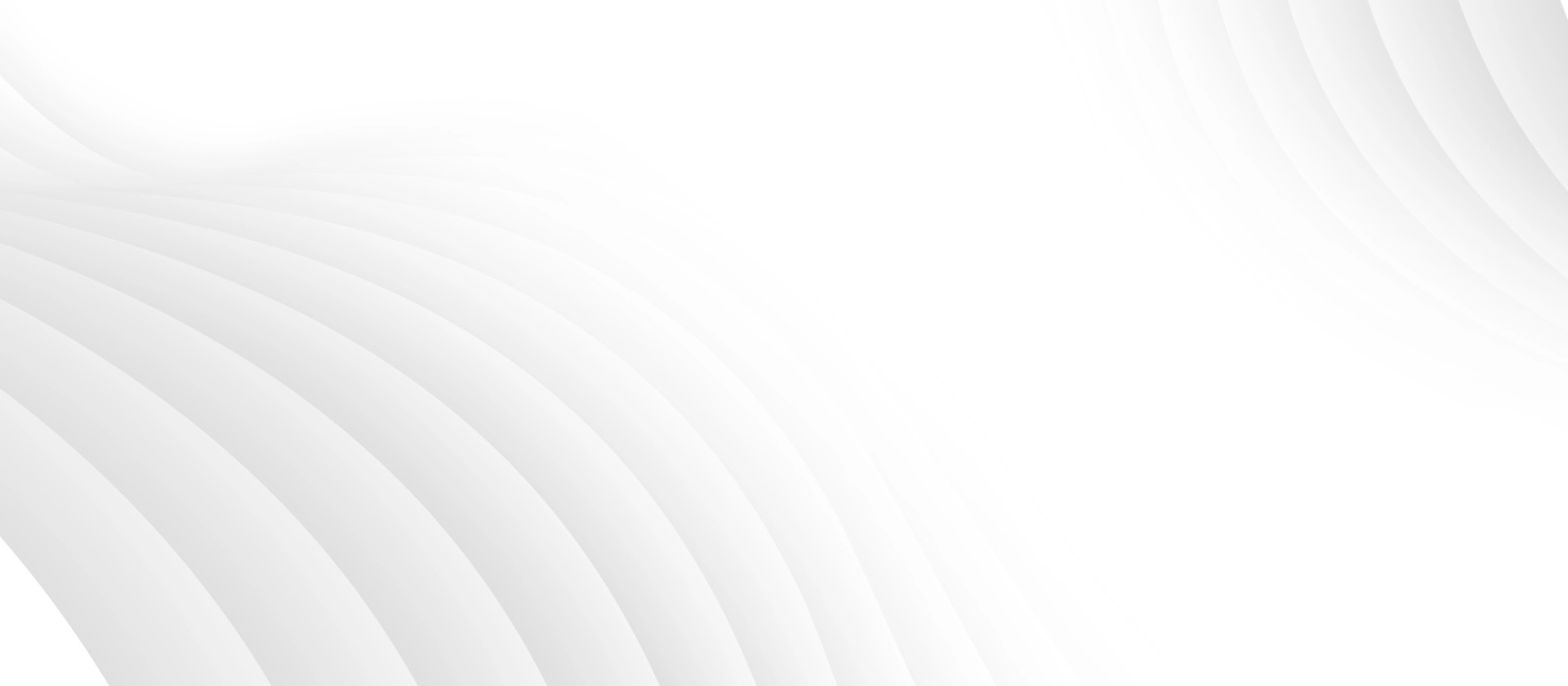
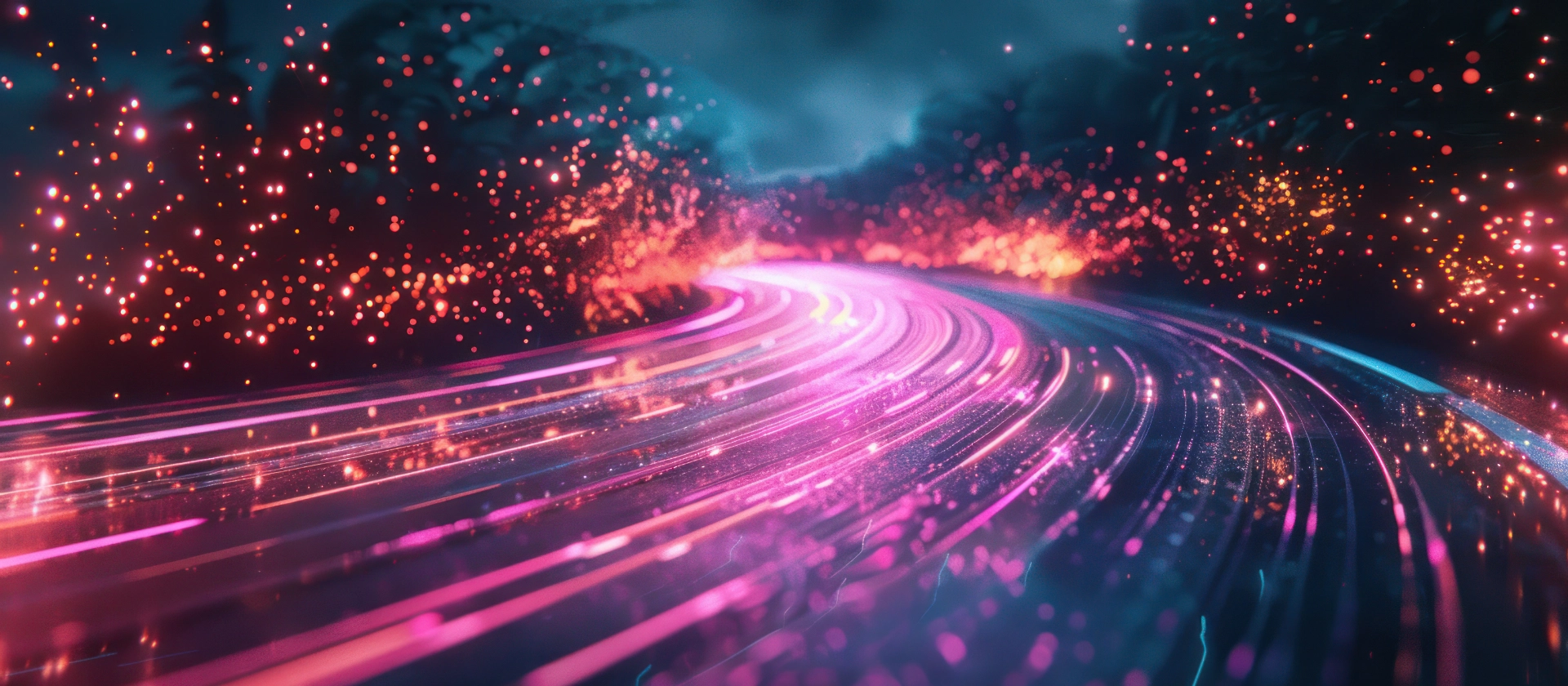
In the race car to data management
The industrial company WAGO implemented the Master Data Management (MDM) platform from Stibo Systems, but did not utilize the potential that the platform offers. The company therefore brought msg on board.
Customer
The WAGO Group is one of the world's leading suppliers of connection and automation technology and interface electronics. The family-run company is the world market leader in the field of spring clamp technology. WAGO products and solutions ensure safety and efficiency in industry, in railroad and energy technology, in the marine and offshore sectors as well as in building and lighting technology. WAGO employs around 8,600 people and achieved a turnover of 1.19 billion euros in 2021.
Initial situation
Consolidating product information and providing it to customers and partners in high data quality is of enormous importance to WAGO. A product information management system (PIM) is used to map the broad and sometimes complex portfolio centrally and up-to-date. However, when WAGO's provider discontinued its product, a new system was needed and the decision was made in favor of Stibo Systems STEP. Because: “STEP is very well established and has excellent references,” emphasizes Karsten Urban, Head of Customer Facing IT at WAGO.
WAGO began introducing the software in summer 2017. Once a minimum viable product (MVP) had been introduced and secured, WAGO initially had to contend with some performance difficulties and acceptance problems within the workforce. The platform was usable and access authorizations were granted. However, this generic introduction simply did not meet WAGO's requirements.
WAGO needed a partner who could master the extensive possibilities offered by the Stibo Systems solution. The contact to msg even came about directly through Stibo Systems. “msg is one of the best trained partners we have in the DACH region,” explains Sascha Orth, Head of Account Management for EMEA at Stibo Systems. That's why he established contact between the two companies at the Stibo Systems Connect Conference 2019 in Copenhagen and got the ball rolling.
Solution
The collaboration initially involved the analysis and optimization of product master data and maintenance processes as well as the description of the roles involved in this process. One of the first steps was to carry out a so-called “health check”. The purpose of this was to identify and list existing problems in the implementation and use of STEP. The results formed the basis for making recommendations and developing a plan for redesigning the solution. “Some uncomfortable things came to light,” says Urban. “For example, some weak points in the data structures.” To solve these problems, the WAGO and msg team optimized the IT architecture and the data model. For example, the number of asset types (electronic artifacts and descriptions of a product) was significantly reduced from 120 to nine and interfaces were improved.
A new start for the process
At the same time, msg and WAGO worked together to start the process. “We had pure functionality. We first had to properly model and record the process world and the workflows for the individual employees,” explains Thomas Brandstätter, Head of Product Experience Management at WAGO. This is why WAGO employees, who work with the solution on a daily basis, came together with the experts from msg in workshops. Together, this working group defined the basic processes as well as a responsibility matrix, roles and role systems. “It was a fresh start, you could say,” emphasizes Brandstätter. “We had a wonderful technical shell. But what we were lacking was the surrounding technology.”
Intuitive use thanks to a modern web interface
Another goal and sub-project of the collaboration was to develop and introduce a new web interface. The new user interface was to be more structured and directly display the information that is important for the product. This also includes reference knowledge, images and relevant documents. In addition, an optimized administrator interface (Web UI Product Experience Platform) was to make it possible to maintain product information in a more intuitive way. The implementation met all the requirements of a modern, intuitive web interface in the WAGO corporate design.
Benefits
In the three years of cooperation with msg, WAGO has achieved more intensive use of the standard STEP functions. Thanks to the improved interfaces and the use of event processors, all data is now brought together in the web interface and can be conveniently edited. This has increased acceptance. Product managers can now see all data associated with the respective product - even data from upstream systems. This has created real data transparency.
Overall, the higher performance and acceptance of the solution has reduced the maintenance effort and shortened the time to market. “Product managers now have a central point of contact to view the status of a product,” says Urban. Guido Göbel, division manager at msg, adds: “WAGO previously had a Porsche in the garage and only drove it to buy bread rolls - but now they are really exploiting its potential.”
Outlook
These successes are just the beginning of a joint journey. The plan is to automate the translation of product information into 22 languages. Another goal is to record the CO₂ footprint of the products. “We are looking forward to the additional functionalities that the system will bring,” says Urban. “We can now open up new areas and are planning a long-term collaboration with msg.
Your contact
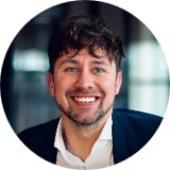