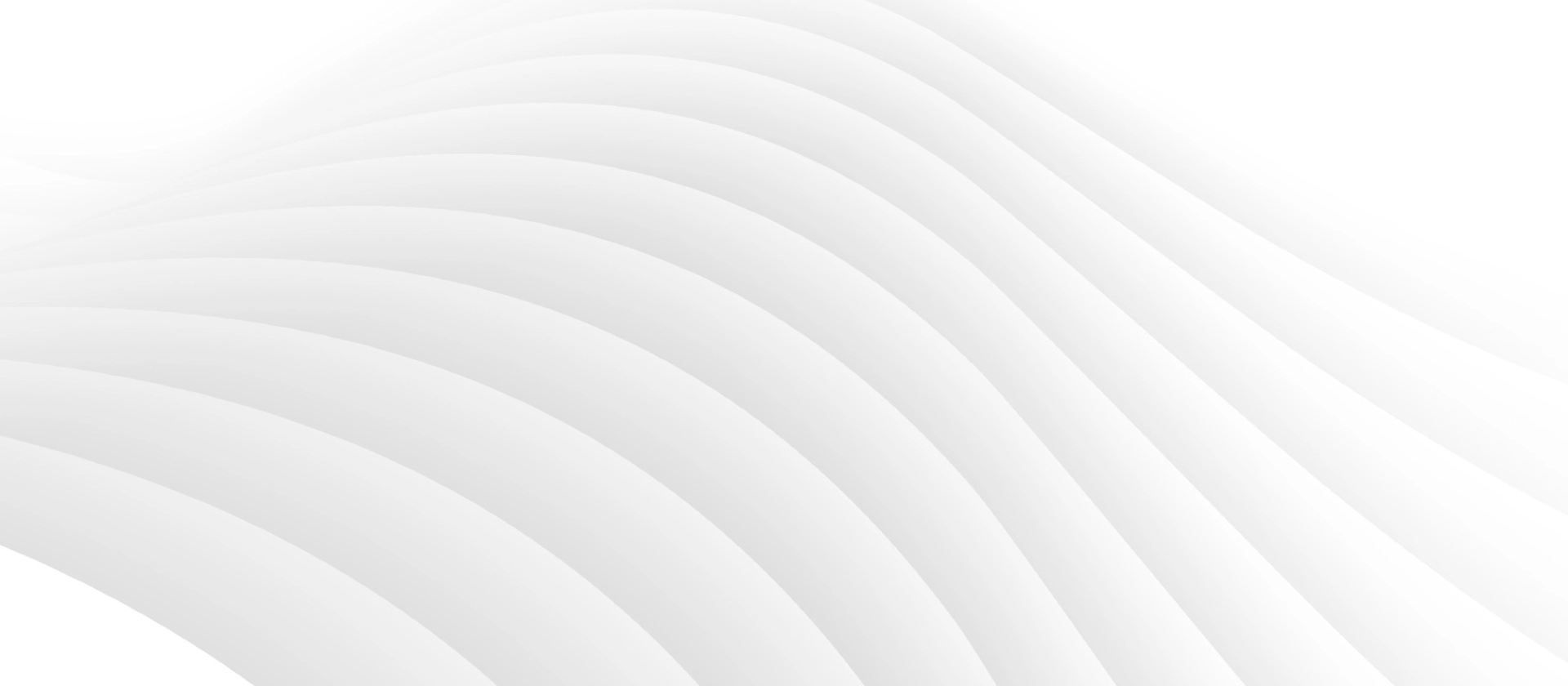
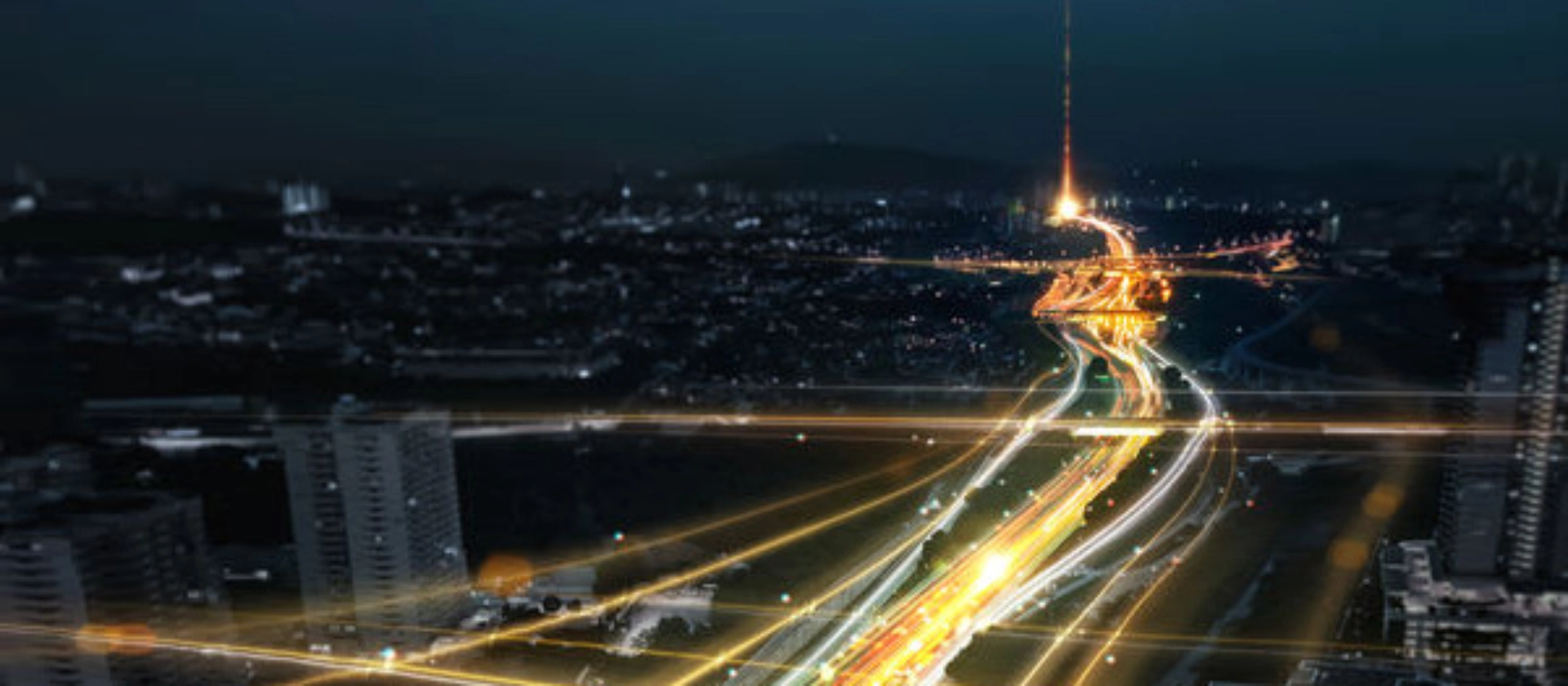
Optimization levers
for successful E/E product data management
New legal regulation for type approval
Automobile manufacturers are under increasing pressure to implement the "Conflicts in Product Data Management in Scheduling Validity" requirement – a UNECE homologation regulation for product data in the field of electrics/electronics (SUMS-11-2). The aim of the UNECE regulation is to harmonize technical vehicle regulations across all OEMs.
From January 2021, the introduction of a Software Update Management Systems (SUMS) will be mandatory for all automotive manufacturers. Without SUMS, no new vehicle types may be approved from July 2022, and no new vehicles produced from this date may be approved from July 2024.
This requirement standardizes test procedures for resolving conflicts in E/E product data management in scheduling validity. This places a legal obligation on automotive manufacturers to efficiently manage and document E/E product data.
Far-reaching consequences for OEMs
The vehicle product is constantly evolving due to changing laws, technical updates and further or new developments. In this context, new vehicle configurations are frequently created in series production.
Currently, these technical changes for hardware and software are not explicitly mapped in the E/E product data as part of the product creation process and traditional model maintenance. Scheduling conflicts arise because technology that belongs together (e.g., components that belong together in terms of scheduling) is not used synchronously. Affected here are change mechanisms of ECUs in the vehicle, which regulate, for example, basic physical TARGET key figures for speed, pressure and temperatures.
To comply with the statutory UNECE requirements in the area of product data management, cost- and time-intensive process adjustments as well as IT adaptations in already existing IT systems are necessary, as well as the introduction of new IT systems if necessary or on a case-by-case basis. In the process chain, all areas can be affected, from change management and the bill of materials to production and customer service.
Probably the greatest challenge for automotive manufacturers is to implement the process-related and IT adjustments consistently and coherently throughout the entire process chain in the most cost- and time-efficient manner.
Success factors in the implementation of the UNECE directive
Efficient control of E/E product data through network releases is a key success factor for the implementation of the UNECE directive.
The synchronized use of technical changes is intended to map not only fixed changes in the traditional model maintenance process, but also short-term changes and production-critical and safety-critical software updates at a common point in time in the E/E product data, and to resolve scheduling conflicts. In this way, technology that belongs together (e.g., components that belong together in terms of scheduling) is used together in a network. In this context, a network can be understood as a network of ECUs ("product version") with all its technically buildable vehicle variants for a vehicle release. In addition, the network can also be regarded as a single network release ("baseline") in which the hardware and software versions for the individual ECU configurations are precisely defined. In this way, it is possible to prevent software changes in the form of bug fixes that would trigger a production stop from being incorporated into production in an uncontrolled manner. This ensures that changes are timed and coordinated in the future.
From our experience, the following aspects are fundamental for a successful implementation:
- Establishing a process by which vehicles with product versions can be represented, developed and controlled is a key success factor for being able to control technical changes efficiently through networks ("product version", "baseline") and to map them in the E/E product data.
- Care must be taken to ensure suitable interaction in series production between the product version-specific application of components in the electrics/electronics area and components of the complete vehicle. Subsequent cost- and time-intensive process adjustments and IT adaptations should be avoided through early harmonization at component level in the electrics/electronics area and in the complete vehicle.
- Early recognition of possible points of contact with previously practiced methodologies at brand and group level is a fundamental contribution to success. Learning curves can be maximized by comparing and evaluating methodologies already in use:
- Are there already recognizable points in time, e.g. along the lines of traditional model maintenance, when many components have a common deployment date with a fixed validity?
- Is there already a constant vehicle level ("network") between these times?
- How is the cycle between these times performed? Can the cycle for the synchronous deployment of short-term changes in the ECU network (e.g., production-critical and safety-critical bug fixes) be based on the cycle of defined changes (e.g., model maintenance)?
- Can previous scheduling procedures for efficient scheduling control be applied through networks for mapping in product data?
The IT, automotive and homologation experts
The msg group has in-depth IT and industry expertise. Experts in the areas of electrics/electronics, UNECE, software update management systems and homologation support you in identifying relevant regulations in the area of E/E product data. We are also happy to advise you on the evaluation of company-specific processes up to the point of obtaining type approval. Whether for consulting, conception, functional specification up to the implementation of IT systems: We are ready to help.