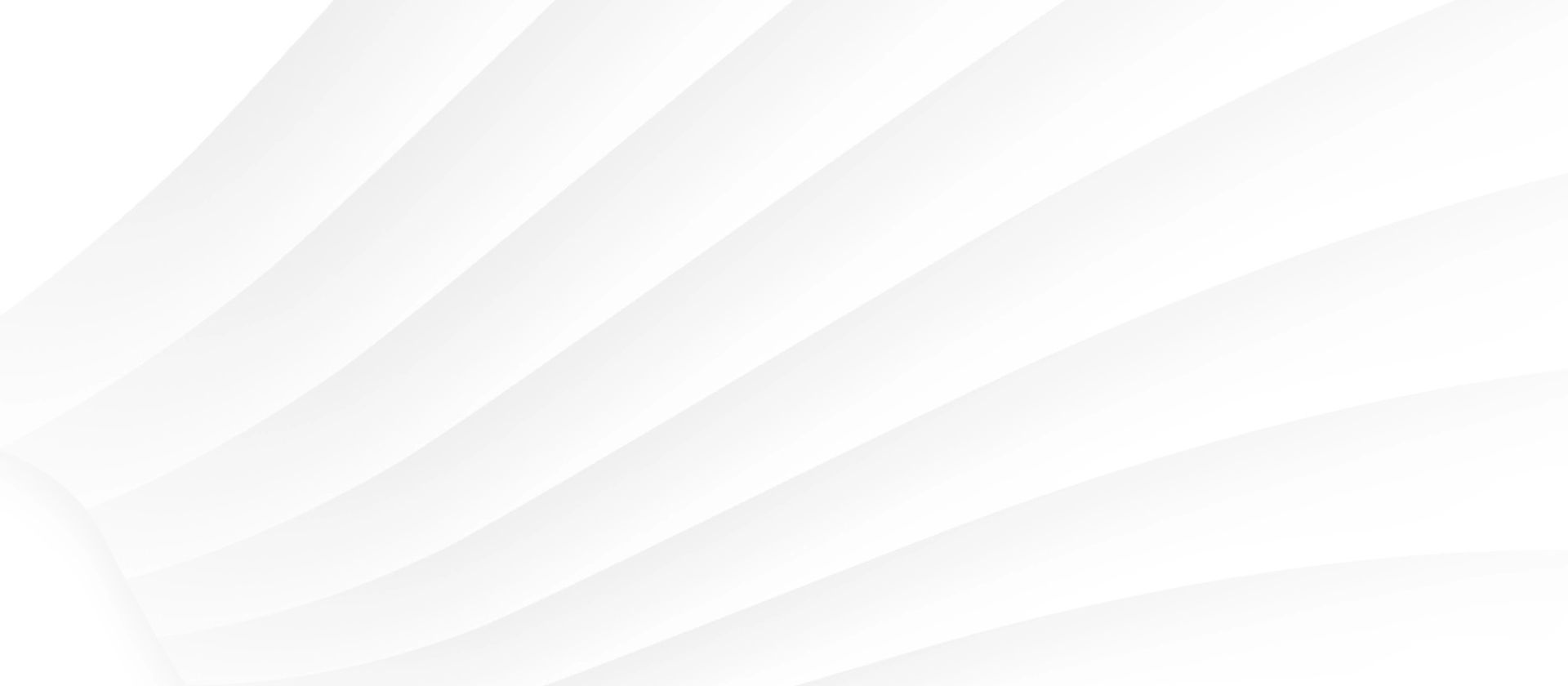
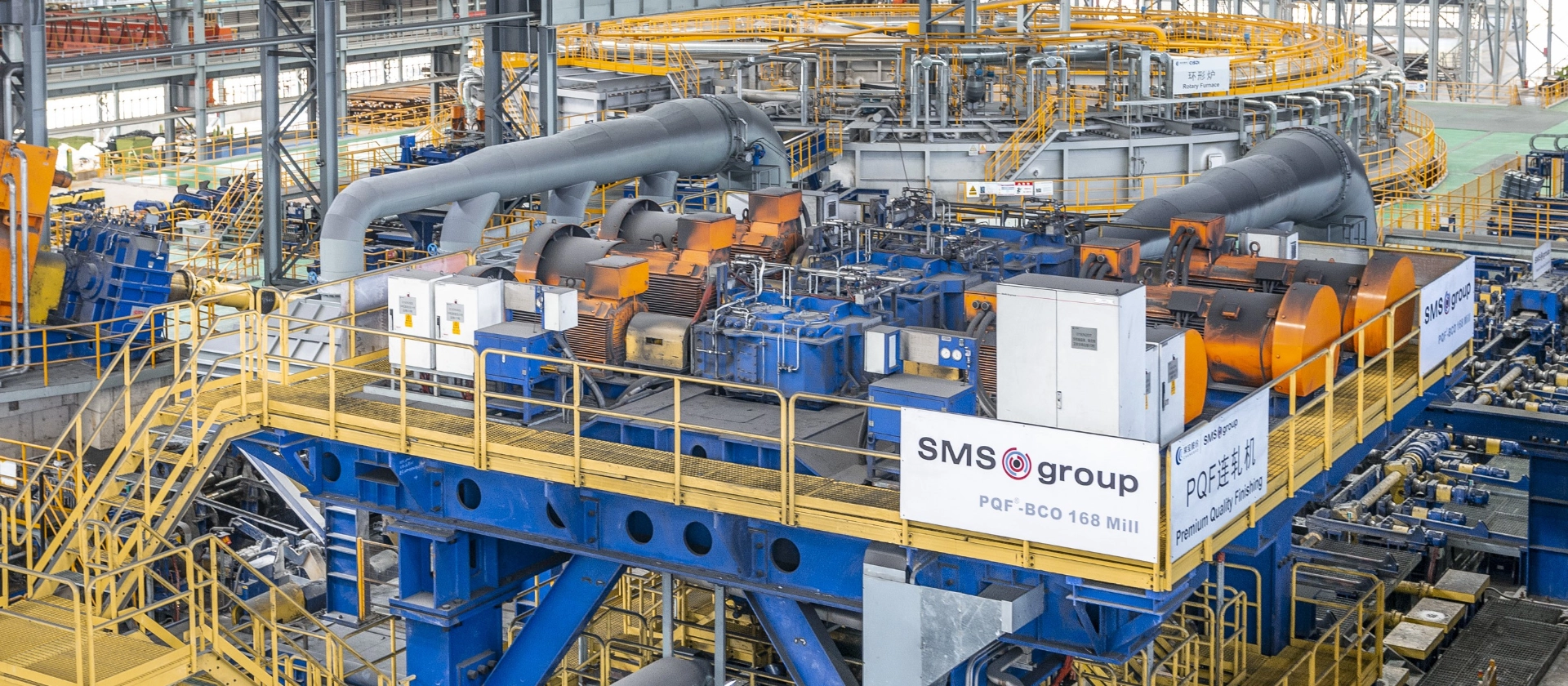
Modernization of plant software
SMS group and msg modernize a 20 year old technology system for seamless tube rolling mills
SMS group planned to modernize its 20-plus years old “CARTA” plant software. For this, a mammoth task had to be undertaken to analyze the organically grown code and develop a suitable solution from ground up. For technical support, SMS group relied on msg. The companies worked in partnership to develop a new version.
Customer
SMS group is an international company in the field of rolling mill technology and plant engineering. Headquartered in Mönchengladbach, the group has offices and production sites in 30 countries. SMS group employs over 14,000 people world-wide and generated a turnover of 3.1 billion euros in 2022.
Initial Situation
In 2016, SMS group has been selling its own CARTA system, a technology system for plant and process optimization, for its seamless tube rolling lines for more than 20 years. Given its long period of use, the software solution had become outdated: Technical problems and limitations were increa-sing, for example with regard to the complex hardware or the dependence on 3rd party software that was no longer being maintained. “The human-machine-interface (HMI) with elaborate client installation was already considered outdated, the connection of further communication partners was very cumbersome and the software solution only supported a BUS system. At the same time, customer requirements, including flexibility in terms of connecting to their systems, have increa-sed significantly,“ reports Alexander Gohr, Senior Technologist for Tube and Pipe rolling, SMS group. “We had to keep pace with that.” In addition, the company was parting ways with its IT service provider at the same time, but had a major order in the USA in mind and needed support quickly. Based on good previous experience, msg was awarded the contract.
Challenge
The CARTA system supports all the different seamless tube rolling mills that have been installed at SMS group customers over the decades. This system was enhanced by additional different functions according to individual customer requi-rements. In some cases, these functions were only used for rare, special plant configurations or even only for individual customers. Some of these enhancements were incompatible in the core and forced a split development process, which further increased the cost and complexity. The software continued to grow over the years and its modernization was no longer feasible. It was therefore decided to redevelop the system from scratch, taking into account the experience gained. The challenge for the joint team of SMS and msg employees was to understand and reproduce a code that was 20 plus years old.
Solution
The new system, which SMS group wanted to develop together with msg, primarily had to be able to do at least what the old system could do. In addition to optimized handling, important requirements included a reduction in effort and complexity compared to the system that had grown over many years. “We noticed that it was becoming increasingly more difficult from project to project to implement new technical challenges with a 20-plus year old architecture,“ explains Mr. Gohr. “In addition, we had maneuvered ourselves into a dependency from certain software and hardware companies.“
To avoid this in the future system, open source solutions and interchangeable hardware components should be used. Experience has also shown that it is better to rely on an easily adaptable system than on a rigid all-inclusive solution.
The first step was to describe the requirements from a functional perspective. In addition, the feasibility had to be analyzed from a technical point of view. A major challenge here was that some of the adaptations and innovations in the old system were not sufficiently documented, as some had been developed directly by the customer. In short sprints, the team therefore iteratively scrutinized the individual modules and tried to understand decisions and replicate the functionalities 1:1. Initially, the focus was on the plant types of the SMS group with the greatest market demand. For this, feature by feature was implemented until the first product was completed. In doing so, the operation concept was revised and technical innovations integrated. In 2019, around a year and a half later, this product was presented to the customers for the first time. The feedback was immediately positive: Customers liked the new clarity and simplification of process control and process planning. By modernizing the technical basis and exploring the status quo for software solutions, many new „low-hanging fruits“ could also be taken away. The use of modern databa-ses and their replication capability reduced the emergency switchover of the production system from ten minutes to just a few seconds.
Benefit
The new system has many advantages for SMS group and its customers. The streamlined and modernized technology stack, from software to hardware, enables a high indepen-dence from sub-suppliers and third party manufacturers. With focus on transparency and security, the hardware condition is now monitored in real time and problems are reported at an early stage. In addition, the improved backup process and the hardware redundancy enable even more secure operation. The web-based human-machine-inter-face with adjustable access control enables a quick and simple implementation and scaling at the customer‘s site. The revised workflow, the detailed visualizations and the enhanced statistics now offer the customer a better insight and more control over the processes. This all leads to a more affordable, flexible and stable system.
Outlook
In the future, the remaining modules are to be integrated into the new “CARTAneo” system and this is to be completed for all other variations of seamless tube rolling mills. Another future project is to develop the software into a self-learning system: This would then collect statistical data for each rolling operation and independently adjust the settings so that the machines work as efficiently as possible. “We now see the opportunity to make substantial improvements,“ says Mr. Gohr. “This is the way that we want to go. And we will continue to do so with msg.“